blacksheep-1
Epic Contributor
- 6,847
- 9,132
Ok, so Superbeater ate a pinion bearing last track day, it made a couple of laps on the pinion, so I had to cut the inner race off with a death wheel. I have a set of 3.73s along with a build kit, so nows time for the deep dive. To bring you up to speed, I had already changed out axle bearings and replaced the carrier. ( this is the diff where I had to cut the locating pin for the spider gear shaft to get it apart. So all of that is new.
So I pulled out the diff box and got started.
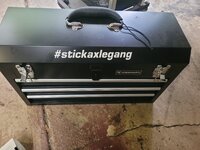
So I pulled out the diff box and got started.
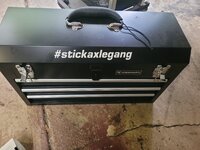